There are many female faces at Sampierana, and this in itself is a source of pride for us. However, one stands out from all the others, perhaps because of her commercial role or perhaps because, when Patrizia talks about excavators, she manages to explain them with disarming simplicity and enthusiasm. It took us two years to convince her, but in the end, we managed to interview her and find out when it all began.
How did your work adventure at Sampierana begin?
It was more or less this time of year, April-May, and the year was 1995. I had finished high school and was working at a company in Cesena, but I wasn’t feeling satisfied. At that moment, I found out they were looking for a reception figure here at Sampierana.
I knew the company because I grew up in these parts. When I introduced myself, they asked me if I knew a bit of languages, mainly English and French. Sampierana at the time was a company of 30 people, and I, fresh out of high school, said yes instantly.
After a few months, however, I was given the opportunity to do something else, which was to get in touch with customers.
And so your commercial adventure began at Sampierana.
Initially, I was responsible for managing orders for the Italian market, with some hesitant approaches to the export market, mainly related to trade fair contacts in neighboring countries (France, Spain), always in the commercial sphere.
Initially, I didn’t think I would stay; I thought I would go to university, that it was a temporary experience, but instead, contact with customers excited me right away, and here I still am.
When did you start traveling in your role as Eurocomach international sales representative?
The turning point came after many years of back-office work, mainly with the 2009 crisis. That year, the Italian market entered a crisis, and we tried to expand our scope beyond the Peninsula and looked for work opportunities everywhere. We even went to Australia and New Zealand. It was essential to broaden our scope to continue working and growing as we had done until then
When you started, were you one of the few female figures in the company?
Yes, at the time, there were few of us. For commercial roles, mostly male figures were sought. After all, the earthmoving sector is primarily made up of men. However, this doesn’t mean there isn’t room for women who want to assert themselves. Potential clients, at the beginning, might have been a bit wary.
if you’re a woman, they tend to constantly put you to the test, so you have to earn their trust. Once earned, you then have to maintain that trust over time, and for this, precision and responsiveness – characteristics perhaps more feminine – which clients recognize and appreciate in me, are absolutely indispensable.
In all of this, what do you think is the greatest achievement?
When they ask you for an opinion, it means you’ve become a point of reference.
A customary question: how did you learn about mini-excavators?
We built our knowledge of mini-excavators in the field, myself included. I was fortunate enough to learn things little by little and also to see the production, to interact with customers at trade fairs. Gradually, I built up my product knowledge, which, it must be said, passionate me, and that’s not a minor factor. Back then, I would go down to the test field near the company, turn on the machine, and enjoy operating the various controls.
I believe this is what helped me: the curiosity to understand the ‘why’ behind things and the daily, direct interaction with the customer.
Do you think that today, with more information available, those approaching machines – both sales personnel and technicians – are less inclined to get hands-on with them?
Yes, today there’s truly a different way of seeing things. I stand by my idea: touching things firsthand helps you understand them better. I’d like to see young people go beyond just being in front of a screen, perhaps see them trying to physically test those famous AUX that are always talked about.
Do you remember when Sampierana started producing mini-excavators?
When Eurocomach was founded, it didn’t make excavators; it made articulated backhoe loaders, a product that has become less and less common over time. For excavators and skid steer loaders (or skids), we initially purchased from Japanese or Korean manufacturers.
However, these machines did not meet the characteristics of the Italian and European markets. Thinking about what to do, during a meeting, this idea came up: why don’t we make our own? The first Eurocomach mini-excavator model entirely designed and produced in Sampierana was the ES500ZT model; the project manager was Engineer Giuseppe Fabbri, and the machine was presented at an important industry fair, SAIE in Bologna, in October 2004.
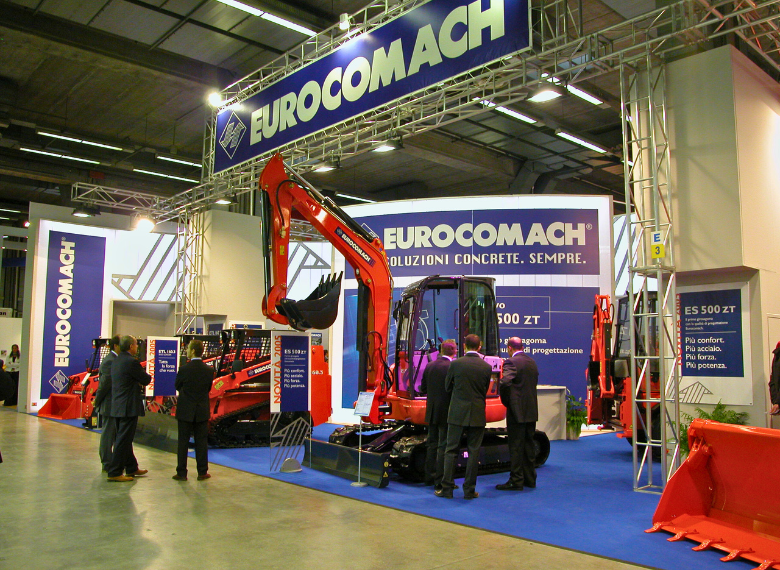
And was this the first one you sold?
Yes, it was the first one entirely made by us, and it was a beautiful, well-made, high-performing machine that gave us a lot of satisfaction.
That first unit was meant to help us understand if we were on the right track. The impact was very positive, and from there, we understood that we could launch ourselves, always with the idea of staying within the compact line, and that we should invest more in mini-excavators rather than backhoe loaders (terneh).
Today, among Eurocomach products, which do you think are the strongest?
The market is in a particular moment, but in my opinion, the range of small mini-excavators from 1 to 2 tons has more potential and better meets market needs, and then I continue to have great confidence in the triple booms, in the TRs; if you can make the customer understand the product’s validity, there’s no comparison.
Even for the 8-10 TON mini-excavators with the new electronics, the response has been positive.
How many years have you been working at Sampierana?
I’ve been at Sampierana for 30 years.
If you were to expect something new in your future at Sampierana, what would you expect?
n my opinion, Sampierana as a company has important potential and characteristics to continue producing for many years. Thanks to CNH, the lines have been strengthened, and everything has been organized so well that I see a large production capacity ; it’s clear that the machines, however, need to be sold, and there’s a lot to do here, the competition is fierce.
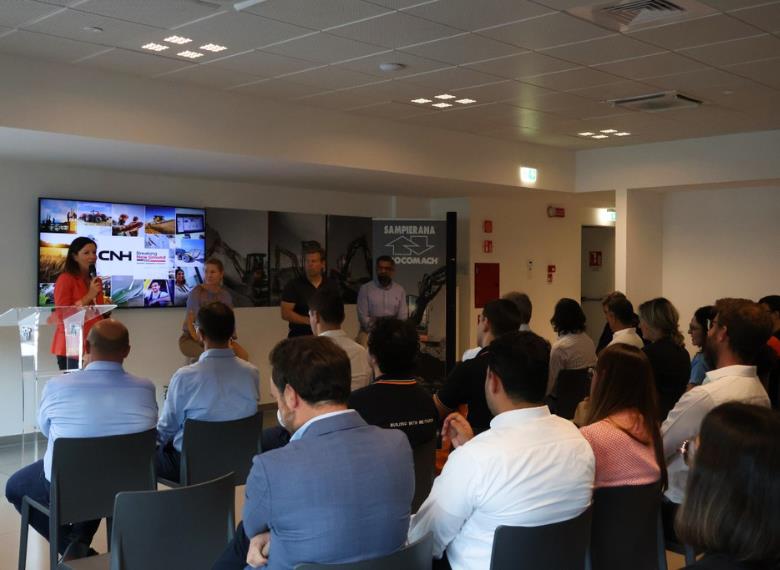
Before retiring, would you be happy to see another Patrizia at Sampierana?
I would be delighted if some of the girls would launch themselves into the commercial side. I also understand that it’s not simple, because the classic commercial role requires you to be out, to travel, and it can be difficult to combine with family life. Sometimes, however, it’s enough to make a first attempt, almost by chance, as it was for me, and anything can happen!